¿Está preparado el mercado para la estandarización de la gestión de baterías en los nuevos vehículos eléctricos? Bart De Cock, Product Manager en ON Semiconductor, Serge Peeters, Business Developer en VITO/EnergyVille y Jeroen Büscher, Product Manager en VITO/EnergyVille nos explican cómo llegar a conseguirlo.
Un paquete de batería de iones de litio (Li-Ion) típico en un vehículo eléctrico (VE o EV) o híbrido eléctrico enchufable (VHEE o PHEV) se compondrá de una cadena en serie de unos elementos de batería (por ejemplo, celdas o celdas en paralelo). Las celdas Li-Ion requieren una monitorización minuciosa de la tensión y la temperatura por medio de un sistema de gestión de batería (Battery Management System – BMS).
El control térmico es un requisito indispensable durante la carga y descarga de las baterías Li-Ion, ya que su temperatura debe mantenerse dentro de la ventana operativa. Las baterías Li-Ion necesitan estar “templadas” con la misión de poder trabajar, pero generan calor cuando se encuentran en uso, por lo que el BMS tiene que ser capaz de calentar y enfriar las propias baterías o, al menos, monitorizar su temperatura por estas razones. Hoy en día, prácticamente cualquier OEM, fabricante de sistemas de batería tier-1 y vendedor de silicio dispone de su propia solución BMS.
Ante el previsible aumento del número de VHEE que circulan por las carreteras a lo largo de los próximos años, cualquier variabilidad en la cadena de suministro de hardware de BMS se convertiría en un serio problema. Los crecientes volúmenes y las modificaciones en los parámetros técnicos y económicos podrían imponer un cambio de proveedor de silicio de BMS. Sin embargo, como los fabricantes de silicio no ofrecen hardware compatible, seleccionar otro chip para el BMS actualmente conlleva que los tier-1s y los OEM hagan frente a un ciclo de redesarrollo y recalificación de larga duración y, en consecuencia, a grandes inversiones y riesgos asociados a la validación y la cualificación.
Será todo un reto alinear a los proveedores de silicio en lo que se refiere a una operación detallada “en el interior del chip” porque cada equipo de desarrollo de los fabricantes posee su propia IP. Afortunadamente, no se requiere una alineación total, siempre y cuando todas las soluciones ofrezcan datos similares (por ejemplo, a través de registros) al controlador host. Para los tier-1s y los OEM tiene sentido disponer de acceso a los circuitos integrados de diferentes marcas que se comportan de manera parecida con respecto a las principales funciones, usando una interfaz de sistema estándar.
Esto se podría ampliar para incluir el enfoque topológico adoptado a la hora de cumplir los requisitos de Seguridad Funcional (Functional Safety – FuSa) como, por ejemplo, el estándar IS0 26262.
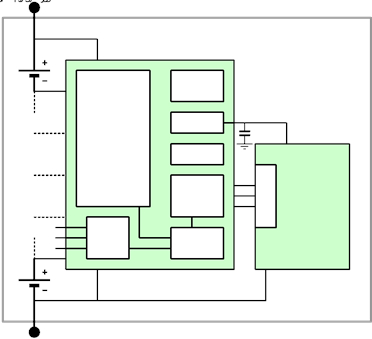
Al examinar las ventajas y las desventajas de las diversas topologías de BMS actualmente disponibles en el mercado, resulta evidente que las diferencias entre las soluciones se encuentran al responder a preguntas como: ¿debe ser un BMS modular (por ejemplo, un CI monitoriza una serie de múltiples elementos de batería) o un BMS a nivel celda (por ejemplo, un CI controla un solo elemento de las baterías)?; ¿tiene que usar una red cableada o inalámbrica?; y ¿cuenta con un microcontrolador o con una máquina de estado finito? Aunque cada uno de las topologías se merece el derecho a existir, se aceleraría la adopción en el mercado si hubiera estándares disponibles que aborden cada uno de estos puntos y mucho más.